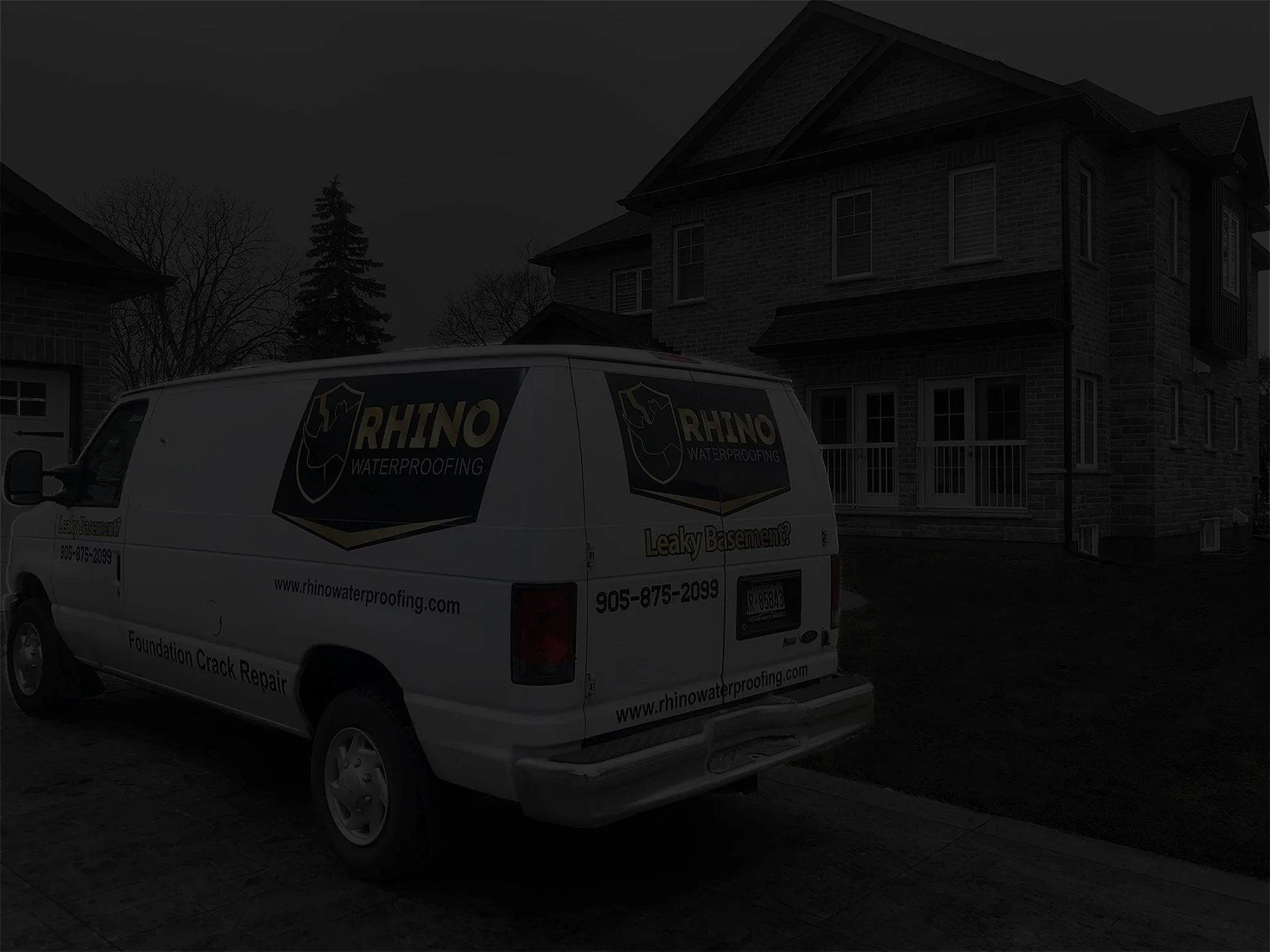
Trust Rhino with all your Basement Waterproofing
& Foundation Repairs
Licensed & Insured
Our Services
-
Foundation crack repair is a crucial aspect of maintaining the structural integrity of a building or home. These cracks can develop due to various factors such as settling of the foundation, hydrostatic pressure, or soil movement. Repair methods typically involve filling the cracks with epoxy injections, polyurethane foam, or utilizing carbon fiber reinforcements to prevent further damage and stabilize the foundation. It's essential to address foundation cracks promptly to avoid potential structural issues and ensure the long-term stability of the building or home. Professional assessment and repair are recommended for effective and lasting solutions.
-
Foundation cracks can indicate various issues with a building's foundation, ranging from minor settling to serious structural problems. Here are some common types of foundation cracks:
Vertical Cracks: These cracks typically run straight up and down and are often caused by settling or shrinkage of the concrete.
Horizontal Cracks: Horizontal cracks are usually more serious and can indicate significant pressure against the foundation walls. They may be caused by expansive soil, hydrostatic pressure from water buildup, or other structural issues.
Diagonal Cracks: Diagonal cracks can occur at a 45-degree angle and may indicate differential settlement or soil movement. These cracks should be inspected by a professional to determine the cause.
Stair-Step Cracks: Stair-step cracks typically occur in brick or block foundations and follow the mortar joints. They are often a sign of settling or movement in the foundation.
Hairline Cracks: Hairline cracks are thin and typically less than 1/8 inch wide. While they may not initially seem problematic, they can widen over time, especially if left untreated.
Cracked Corners: Cracks that form at the corners of windows, doors, or the foundation itself may indicate stress concentration points or settling.
Bulging or Bowing Walls: While not cracks per se, bulging or bowing walls can indicate significant structural issues, often caused by lateral pressure from soil or water.
Cracks Near Basement Windows: Cracks that form around basement windows can indicate water pressure against the foundation walls, especially if accompanied by signs of water infiltration
It's important to note that the severity of foundation cracks can vary, and not all cracks necessarily indicate a serious problem. However, it's always advisable to have any cracks inspected by a qualified professional, such as a structural engineer or foundation specialist, to determine their cause and the appropriate course of action.
-
Epoxy Injection: This method involves injecting epoxy resin into the crack to fill and seal it. Epoxy is a durable material that effectively bonds with the concrete, restoring the structural integrity of the foundation.
Polyurethane Injection: Similar to epoxy injection, polyurethane foam is injected into the crack, expanding to fill voids and create a watertight seal. This method is particularly effective for actively leaking cracks.
-
Rhino Carbon Fiber Reinforcements are a type of structural reinforcement system used to repair and strengthen cracked or bowed foundation walls. These systems utilize carbon fiber materials, which are known for their high strength-to-weight ratio and durability. Here's an overview of Rhino Carbon Fiber Reinforcements and how they work:
Material: Rhino Carbon Fiber Reinforcements consist of carbon fiber straps or strips. Carbon fiber is a strong, lightweight material made from carbon atoms bonded together in a crystal alignment. It is known for its exceptional tensile strength and resistance to corrosion.
Installation: The installation process typically involves preparing the surface of the foundation wall by cleaning and prepping it. Then, epoxy adhesive is applied to the wall surface, and the carbon fiber straps are securely bonded to the wall in a grid-like pattern. The installation process is relatively quick and minimally invasive compared to traditional foundation repair methods.
Function: Once installed, the carbon fiber straps provide additional reinforcement to the foundation wall, helping to prevent further cracking or bowing. They distribute the structural load more evenly across the wall surface, reducing stress concentrations that can lead to further damage.
Flexibility: One of the advantages of carbon fiber reinforcements is their flexibility. They can accommodate slight movement in the foundation without compromising their structural integrity. This flexibility helps to ensure long-term stability and performance.
Appearance: Rhino Carbon Fiber Reinforcements are designed to be low-profile and unobtrusive once installed. They can be painted over to blend in with the surrounding wall surface, providing a clean and aesthetically pleasing finish.
Effectiveness: Carbon fiber reinforcement systems, including those from Rhino, are widely recognized for their effectiveness in strengthening foundation walls and preventing future damage. They are often used in both residential and commercial applications to address various types of foundation issues, including cracking, bowing, and settling.
Overall, Rhino Carbon Fiber Reinforcements offer a durable and reliable solution for reinforcing foundation walls and addressing structural issues. However, it's essential to consult with our qualified foundation repair specialist to assess the specific needs of your property and determine the most appropriate repair strategy.
-
Rhino Carbon Fiber bowed wall repair systems are specifically designed to address bowing or leaning foundation walls. When a foundation wall begins to bow or lean inward due to external pressure from soil or water, it can lead to structural instability and potential damage to the building. Rhino Carbon Fiber systems provide a solution to reinforce and stabilize these walls.
-
An interior drainage system with a sump pump is a common solution for managing basement or crawl space moisture and preventing water damage in residential and commercial buildings. This Method of basement waterproofing is typically installed for block foundations or areas of high water table. Here's how it typically works:
Installation of Interior Drainage System: The first step involves installing a drainage system along the interior perimeter of the basement or crawl space. This system is usually comprised of perforated pipes or drains installed beneath the floor slab or along the base of the walls. These pipes are designed to collect and redirect water seepage or groundwater that may enter the space.
Collection of Water: As water enters the basement or crawl space through cracks, gaps, or hydrostatic pressure, it is directed towards the interior drainage system. The perforated pipes or drains collect the water and channel it towards a central collection point.
Sump Pump Installation: At the lowest point of the drainage system, a sump pump pit is installed. This pit houses the sump pump, which is a mechanical device designed to pump water out of the basement or crawl space. The sump pump is typically equipped with a float switch that activates the pump when water reaches a certain level in the pit.
Water Discharge: Once the sump pump is activated, it pumps the collected water out of the pit and away from the building through a discharge pipe. The discharge pipe is routed to a location where the water can safely drain away from the foundation, such as a storm drain, a dry well, or a designated drainage area on the property.
Backup System (Optional): In areas prone to power outages or heavy rainfall, it's advisable to install a backup sump pump system. Backup systems can include battery-powered sump pumps, water-powered sump pumps, or even generator-powered sump pumps. These backup systems provide added protection against flooding in the event of a primary pump failure or power loss.
Maintenance: Regular maintenance of the interior drainage system and sump pump is essential to ensure proper functioning and prevent potential problems. This may include cleaning debris from the sump pump pit, testing the operation of the pump and float switch, inspecting and repairing any damaged components, and ensuring that the discharge pipe is clear and unobstructed.
Overall, an interior drainage system with a sump pump is an effective way to manage moisture and water infiltration in basements and crawl spaces, helping to protect the structural integrity of the building and prevent water damage. It's important to consult with our qualified waterproofing specialist to assess your specific needs and determine the most appropriate solution for your property.
-
Exterior excavation and basement waterproofing is a comprehensive approach to preventing water infiltration and moisture problems in basements. It involves excavating around the exterior perimeter of the foundation, installing waterproofing materials, and ensuring proper drainage away from the building.
Exterior excavation and basement waterproofing is a significant investment but can provide long-term protection against water damage and moisture problems in basements. It's essential to work with a reputable waterproofing contractor who has experience in exterior waterproofing techniques to ensure the job is done correctly and effectively.
-
Sump pumps are mechanical devices designed to remove water that has accumulated in a sump pit, typically found in basements or crawl spaces. They are essential for preventing flooding and water damage in homes and buildings. A battery backup system for a sump pump provides an additional layer of protection in case of power outages or pump failures. Here's how sump pumps and battery backup systems work:
Sump Pump Operation: The sump pump is installed in a sump pit, which collects water that has seeped into the basement or crawl space. When the water level in the pit reaches a certain height, a float switch or pressure sensor activates the pump.
Water Removal: Once activated, the sump pump begins pumping water out of the sump pit and away from the building through a discharge pipe. The water is typically directed to a storm drain, a dry well, or a designated drainage area on the property.
Power Source: Most sump pumps are powered by electricity and are connected to the home's electrical system. However, during power outages, the pump may be rendered inoperable, leaving the basement vulnerable to flooding.
Battery Backup System: To address this vulnerability, a battery backup system can be installed alongside the sump pump. The backup system includes a rechargeable battery that provides power to the pump in the event of a power outage.
Automatic Switching: The battery backup system is equipped with a control unit that monitors the power supply to the primary sump pump. If a power outage is detected or if the primary pump fails for any reason, the control unit automatically switches the sump pump to battery power.
Alarm System: Some battery backup systems also include an alarm or notification feature to alert homeowners to potential issues with the sump pump or the backup system. This allows for prompt action to be taken to address any problems and prevent flooding.
Maintenance: It's essential to regularly test and maintain both the primary sump pump and the battery backup system to ensure they are functioning correctly when needed. This may include testing the operation of the float switch, inspecting the discharge pipe for blockages, and checking the battery's charge level.
In summary, sump pumps and battery backup systems work together to provide reliable protection against basement flooding and water damage, even during power outages or pump failures. They are crucial components of any home's waterproofing system, particularly in areas prone to heavy rainfall or snowmelt.
-
Foundation parging is a process used to apply a thin coat of mortar or cement-based material to the exterior surface of a foundation wall. Parging serves both functional and aesthetic purposes and can help protect the foundation from moisture, improve its appearance, and provide a smooth base for painting or other finishes. Here's an overview of foundation parging:
Surface Preparation: Before applying the parging material, the surface of the foundation wall must be cleaned and prepared. This typically involves removing any loose debris, dirt, or existing parging material. It may also involve repairing any cracks or defects in the foundation wall.
Mixing the Parging Material: Parging material is usually a mixture of Portland cement, sand, water, and sometimes additives like lime or acrylic. The mixture should be mixed thoroughly to achieve the desired consistency and workability.
Application: The parging material is applied to the foundation wall using a trowel or sprayer. It is spread evenly over the surface in a thin layer, typically ranging from 1/8 to 1/4 inch thick. The parging material should be applied smoothly and evenly to create a uniform finish.
Texturing (Optional): Depending on the desired aesthetic, the parging material can be textured while it is still wet. Common texturing techniques include swirling, stippling, or creating a sand or stone finish. Texturing can help improve the appearance of the foundation wall and provide visual interest.
Curing: After the parging material has been applied, it needs time to cure and harden properly. Curing time can vary depending on factors such as temperature, humidity, and the type of parging material used. It's essential to follow the manufacturer's instructions for curing to ensure optimal performance and durability.
Painting or Sealing (Optional): Once the parging material has cured completely, it can be painted or sealed to further protect the foundation wall and enhance its appearance. Waterproof or elastomeric paints and sealers are commonly used to provide additional moisture resistance and durability.
Overall, foundation parging is a straightforward process that can help protect and improve the appearance of foundation walls. However, it's essential to ensure proper surface preparation and application techniques to achieve a durable and long-lasting finish. If you're not comfortable tackling foundation parging yourself, it's best to hire a professional contractor with experience in this type of work.
-
Basement lowering, also known as underpinning or basement excavation, is a construction process that involves increasing the height of a basement by excavating the existing floor to create additional space. This process is typically undertaken to increase the usable space in a basement or to create additional headroom for renovations. Here's an overview of the basement lowering process:
Assessment and Planning: The first step in basement lowering is to assess the existing foundation and basement structure to determine if it is suitable for excavation. A structural engineer or foundation specialist will evaluate factors such as soil conditions, foundation type, and structural integrity to ensure that the basement can be safely lowered.
Excavation: Once the assessment is complete and necessary permits are obtained, excavation work can begin. The existing basement floor is carefully removed, typically using heavy machinery such as excavators or bobcats. The excavation depth will vary depending on the desired increase in height and any structural considerations.
Shoring and Support: During the excavation process, temporary shoring and support systems are installed to stabilize the foundation walls and prevent collapse. This may involve installing steel beams, bracing, or temporary retaining walls to provide structural support during the excavation.
Foundation Modification: In some cases, the existing foundation walls may need to be modified or reinforced to accommodate the lower basement level. This may involve underpinning, which is a process of strengthening the foundation by extending its depth or width, or adding additional support columns or walls.
Waterproofing and Drainage: Waterproofing and drainage systems are essential components of basement lowering to prevent water infiltration and moisture problems. New waterproofing membranes, drainage pipes, and sump pumps may be installed to ensure a dry and usable space.
New Basement Floor: Once the excavation is complete, a new basement floor is poured or installed at the desired height. This floor may be made of concrete or another suitable material and is typically finished with leveling compound, flooring materials, or other finishes as desired.
Utilities and Services: If necessary, utilities such as plumbing, electrical, and HVAC systems may need to be relocated or modified to accommodate the lower basement level. This may involve rerouting pipes, wiring, or ductwork to ensure proper functionality and accessibility.
Finishing and Renovation: Finally, the newly lowered basement space can be finished and renovated according to the homeowner's preferences. This may include installing walls, ceilings, flooring, lighting, and other amenities to create a functional and comfortable living space.
Basement lowering is a complex and labor-intensive process that requires careful planning, engineering expertise, and skilled construction work. It can significantly increase the usable space and value of a home but should only be undertaken by experienced professionals to ensure safety and structural integrity.
description
Rhino Carbon Fiber The Strongest Wall Repair System On The Market
Need an Estimate?
Fill out the form below and we will get back to you.
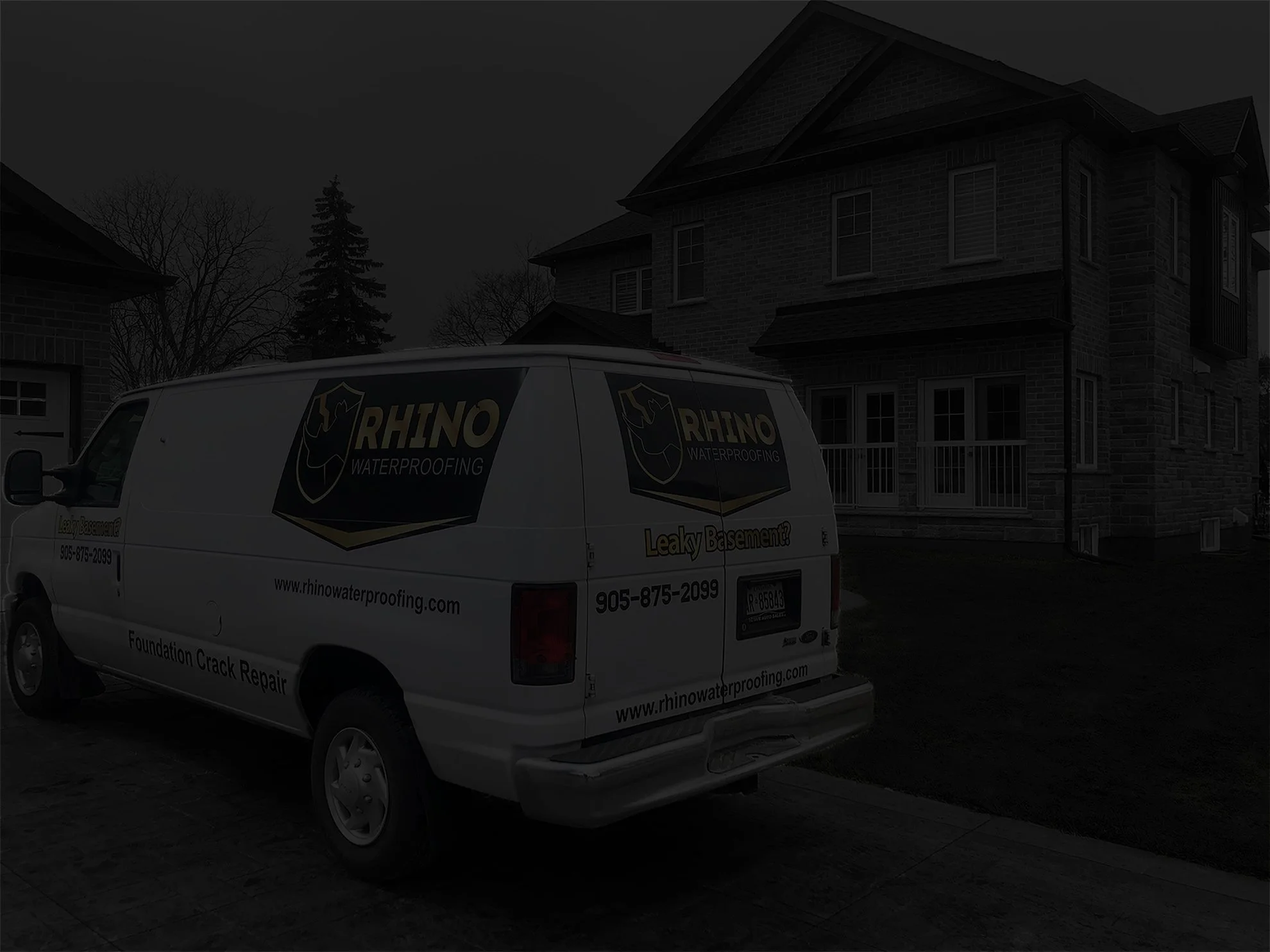
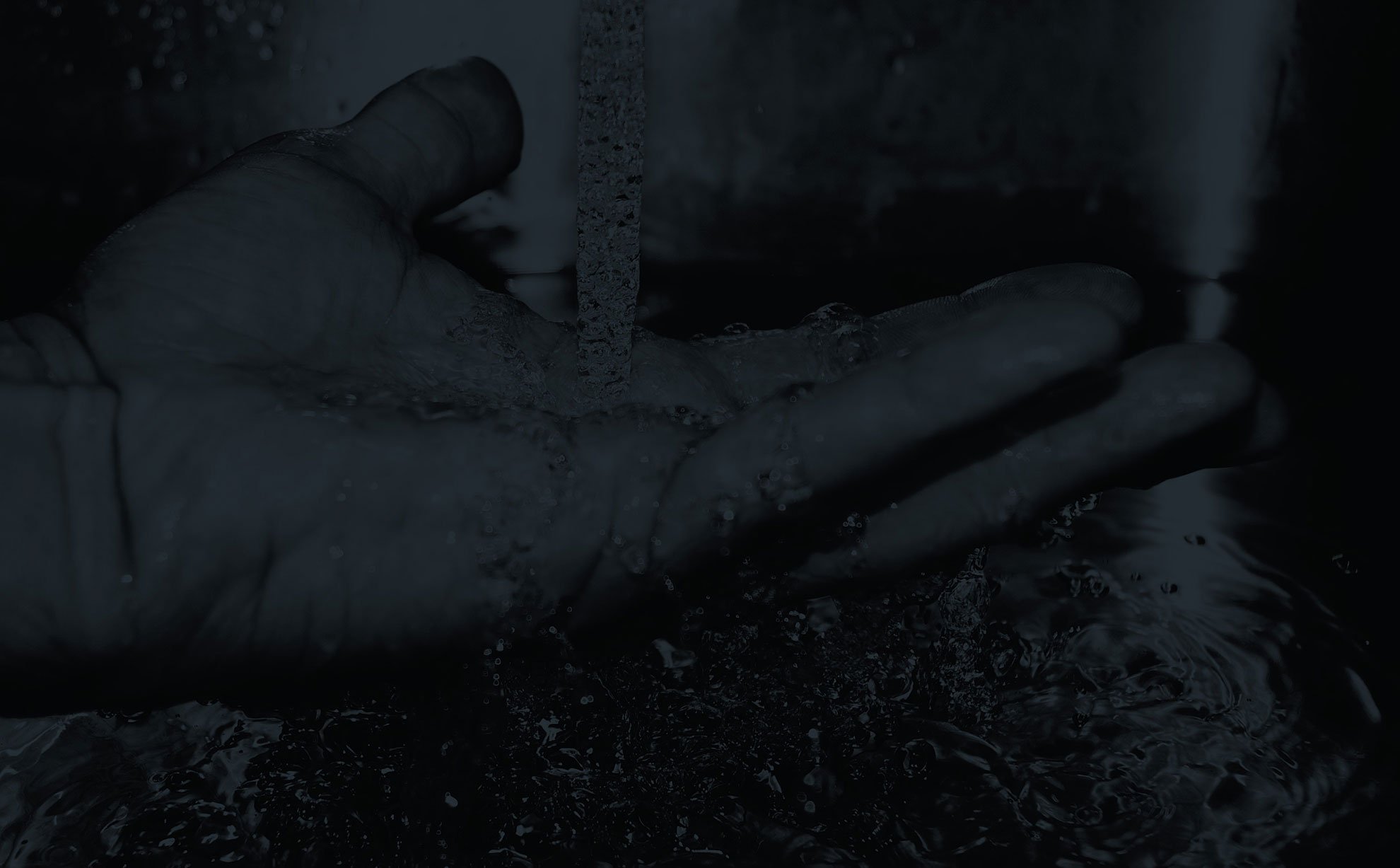
